- Reliability is the Key
- Lifetime Costs Lower with Copper
- Cost of Copper “Not a Big Factor”
- High Efficiency with Copper
Allegheny Power, a unit of Allegheny Energy, is a regulated utility that delivers power to about 3.5 million customers in parts of Pennsylvania, Maryland, Virginia and West Virginia. Its customer base is mostly rural. Many segments of its distribution system are radial feeds, while other segments serve industrial loads that can fluctuate widely. Maintaining maximum system reliability under conditions like that is very important, even if it isn’t always easy. But the company found that one surefire way to keep the lights on — and keep its customers happy — is by buying only copper-wound transformers for its substations.
Ask Joe Leighty. He’s the engineer in Allegheny Power’s support unit responsible for designing substations and specifying transformers, a job he’s held for more than 20 years. Leighty has seen how utility transformer preferences have changed over the years and, from those changes, he’s learned what’s important when it comes to ensuring long life in critical equipment (Figure 1).
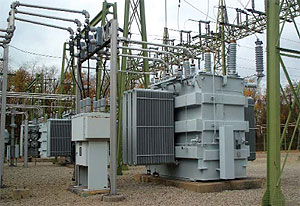
“Our company was incorporated in 1925,” says Leighty, “and we’ve accumulated quite a mix of transformers, some copper and some aluminum. Although we did buy aluminum transformers years ago — and that included everything from small power transformers up to units rated at 765 kV — today, with the exception of small poletop and padmount distribution transformers, we buy nothing but copper transformers.
“We basically use transformers in two size ranges,” Leighty continues. “These include the intermediate-sized power transformers in our substations and the very large units found at generating stations. Much of my work deals with mid-sized transformers rated at 25-kV to 138-kV primary and around 12-kV secondary voltages.
“For example, we just installed a couple of 135.3 kV — 13.2/7.6 kV units at a substation that will serve a new shopping mall north of Pittsburgh. The transformers are equipped with vacuum-driven tap changing to adjust for our variable load. Like all transformers we buy today, these are completely copper-wound (Figure 2).
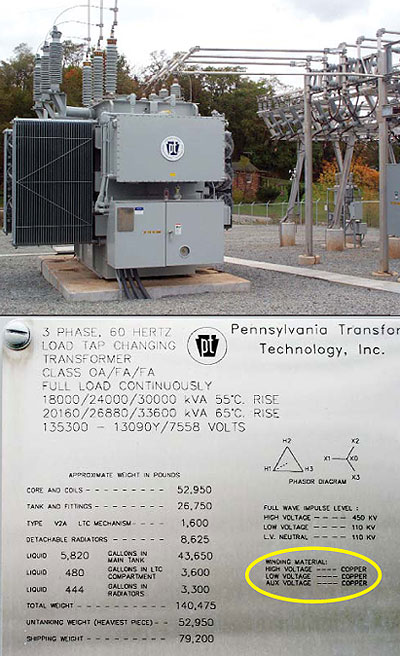
Reliability is the Key
“The main reasons we’ve decided to go with copper are what I call strength issues," explains Leighty. “Copper windings are stronger and better able to handle fault forces than aluminum, so a copper transformer is more likely to survive a big overload. We’re primarily a rural electric company with a lot of radial distribution in our system. If we lose a transformer, it isn’t always easy to switch to an alternate source of power on the grid. A transformer outage can affect people over a very large area, so we have to build maximum reliability into our system.
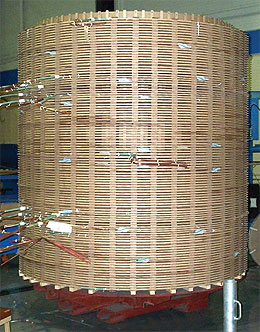
“Thermal expansion is another important issue. The thermal expansion of aluminum is much larger than copper’s from normal ambient temperatures down to –20°F. That’s important because substation transformers are built to a specific design coil height, and coil windings are clamped to keep that height fixed. As our load fluctuates, transformer temperatures rise and fall. The coil wants to compress and expand, but it can’t because it’s clamped. Instead, it compresses the paper insulation between turns (Figure 3). The effect is especially pronounced when a fault occurs, but it affects aluminum windings much more so than it does copper due to the difference in thermal expansion.
“Later, when the temperature returns to normal, the insulation in an aluminum transformer might not be as tight as it was before the overload. That allows the windings to loosen slightly, a condition that might lead to loose connections at some point in time.”
Back to TopLifetime Costs Lower with Copper
Leighty believes copper also helps reduce lifetime ownership costs. “Again,” he says, “it’s due to copper’s higher strength. Life-cycle cost is not just a matter of efficiency (even though that’s important), it’s also a function of reliability.
“For example, we expect a 40- to 50-year life cycle in our transformers. We monitor their condition with periodic oil analyses. When an analysis shows that gas and moisture are increasing, it’s a sign that the oil is breaking down and that there’s probably overheating going on at a connection inside the transformer. If you have aluminum-wound coils, the internal connections can loosen (creep) over time, just like connections in aluminum house wiring did 30 years ago. Loose connections cause the heating that breaks down the oil. We almost always identify the problem before it gets out of hand, but, when we don’t, the result can be catastrophic. Even if we don’t lose the unit, repairs are expensive and not always easy because of the nature of our system. With copper windings, connections stay tight, transformers stay on line, there are fewer repairs and lower ownership costs. It’s almost a nobrainer to go with copper now because of better reliability.”
Back to TopCost of Copper “Not a Big Factor”
But does buying 100% copper transformers increase the utility’s costs? Not according to Leighty. “The cost difference between copper and aluminum is not a big factor in this size range,” he says. “The economics in favor of aluminum just aren’t there. You’ve probably heard about copper transformers being smaller and lighter, that they need less steel and oil, etc. Those factors reduce costs for the manufacturer, but they save us money, too, because a copper transformer lets us build a smaller pad with less concrete and maybe a little less real estate (Figure 2). From a cost standpoint, there is no benefit to go with aluminum.”
High Efficiency with Copper
Like all electric utilities, Allegheny Power is mandated by its regulators to ensure high efficiency in its equipment. Here, too, copper provides a win-win situation. Leighty explains, "We can no longer use A and B values1 anymore to specify an efficiency rating in our transformers because, after deregulation, we had no way of knowing what the power we buy costs to produce. But high efficiency is still very important to us, since deregulation also meant we had to absorb the costs of inefficient equipment. There are many ways we can write our specs to guarantee high efficiency in our transformers — specifying copper is one of them.” Better fault performance, comparable up-front costs, higher reliability, high efficiency and lower cost of ownership: all good reasons why smart utilities like Allegheny Power specify only copper windings in their substation transformers.
The Principals
Joe Leighty is the substation and transformer engineer for Allegheny Power, a unit of Allegheny Energy. His 20 years of experience with both copper and aluminum-wound power transformers prompted him to specify nothing but copper. Mr. Leighty can be reached at (724) 626-6276 and at [email protected].
Footnote
1. A and B values represent the present value cost to a utility, in dollars per kilowatt, of losses in a transformers core (A) and windings (B).